Friday, July 23, 2010
Open Day Video
Thursday, July 22, 2010
Trip To Maine
I’ve always wanted to make the journey to the Lie-Nielsen factory in Warren, Maine – it’s been a dream of mine since I’ve been into woodworking. And while I have met Tom Lie-Nielsen a few times at various woodworking events it’s taken until now for me to realize that dream of a “factory tour”.
So – my trip was multi-faceted. First, a tour of the factory to see how everything was made, seeing the journey from raw materials to the completed tools being packed and shipped. Next a few days training on-site (more on this later) and finally to demonstrate my planes at the open day weekend at the factory, topped off with a Lobster bake!
The Factory
We were staying in Portland, a town about 60 miles south of the toolworks location. So each day started with a coffee and a drive through the beautiful Maine countryside. The factory appears just off the main road in picturesque fashion, and we turn in and park up. The building itself has been extended many times as the company has grown over the years and looked just as I imagined it. Additional buildings have been erected alongside to house more machinery and storage – these buildings were also erected by the staff. During my many chats with staff members it was obvious how proud they were of the facility and the work they do.
We were given a tour of the facility, which has separate areas for storage, tool machining, saw making, handle manufacture, finishing and polishing, blade manufacture and packing. There is a also a handsome shop/display area with all the range of tools on display and available to try out.
Two things that stood out to me most as we were shown around were :
Each family of tools is made by a set team of makers – i.e. all block planes are made by the same team, and they have their own area complete with the tools and machinery they need. There was no “sharing” of machinery – each team had their own area and specialized in their own range of tools.
There was a huge amount of hand work involved in the making of every tool. You imagine that with modern day CNC machinery you would put raw material in one end and finished tools appear magically at the other end – this could be no further away from the truth! There was a small army of workers who specialise in particular skills, and it was quite heart-warming to see.
I was quite amazed to see the saw making shop – this had a collection of interesting machinery. Tooth cutting machines, tooth filing machines, machined modified to perform specific tasks and a man called Patrick. Patrick makes all the Lie-Nielsen hand saws and hand files and tests every single one! We were treated to a saw sharpening demonstration by Tom Lie-Nielsen (on a staggeringly hot day which took ones breath away) and shown the many steps in a saws manufacture – very low tech and definitely not the modern day super efficient production style I was expecting.
The irons for all the Lie-Nielsen planes and shaves are also made in-house. There are many steps in the manufacture, including heat treating, tempering and cryo treatment. There is a small crew of skilled workers who do this work, and throughout the week I was able to watch them at work – it was amazing how many steps were involved in the making a blade the Lie-Nielsen way and also the amount of times each individual blade was checked throughout the process, from grinding the raw blank through to the final hand lapping of the back.
We were treated to a tour of the bench making shop – this is at a separate workshop nearby. It was quite impressive to see huge amounts of maple being turned into accurate and sturdy workbenches. Shop manager Darren is a stickler for perfection and it was very enlightening to see the amount of time and care that goes into each bench.
Tom Lie-Nielsen gave us a sneak preview of many of the tools soon to be reaching production, as well as some interesting ideas he has in the pipeline. I’ve been sworn to secrecy, but there some real treats ahead!
As I mentioned earlier, I was at the factory for a few days training on too demonstrating. We had three days tuition from Deneb Puchalski , aided by the team of L-N demonstrators Alex, Lee, Curtis and Jeremy (apologies if I missed anyone!). It was very enjoyable, despite the high temperatures and humidity of the Maine summer, and I came away topped up with information, ideas and enthusiasm. Expect to see me at a woodworking show near you demonstrating these great tools soon!
The final days of my trip were the “open day” event. The factory was thrown open to the public, with tool demonstrations from Lie-Nielsen as well as other craftsmen like Michel Auriou, Chris Becksvoort, Al Breed, Kevin Drake and myself. It was a busy couple of days and it was great to meet and talk to so many passionate American woodworkers. The finale of the open day was the “Lobster Bake” – fresh Maine lobster and mussels cooked on a barbeque at the rear of the factory! Boy did that taste good (washed down with a cold beer!) A great way to end the week.
After reflecting on my trip the main thing that stood out to me was the tools – Lie-Nielsen tools are made with care and attention, with huge amounts of hand work by a hard working team of American workers. The factory was much closer in spirit to the way I work in my one-man workshop that to a modern production factory and I am amazed that they are able to sell their beautiful tools at such reasonable prices and still make a modest profit. Truly these are “heirloom” tools, tools to be proud and worthy of a place in our tool chests.
My thanks again to Tom and his wonderful staff for looking after us so well on this trip.
Cheers
Philly
Wednesday, July 07, 2010
More partidge wood...
I've got a fair selection of exotic timbers hoarded away in the workshop. Small pieces, not-so-small pieces and many different types. One I've been wanting to use is Partridge wood - I don't know much about it but I do know its extremely dense. And yes, it does sink in water - I've tried! Recently I made a 2 inch wide smoother for myself from this timber and was very impressed with the beautiful grain - supposedly the timber gets its name from the way the grain resembles partridge feathers. A customer called to place an order recently and mentioned this plane after seeing it in this blog. After searching through my timber store I found a single piece just big enough for a plane and wedge, so the customer was very pleased (and so was I to be using this lovely timber again).
Here's a shot of the plane before any shaping is done on the body - I cut all the important stuff first and do the fun shaping stuff when everything fits and works.
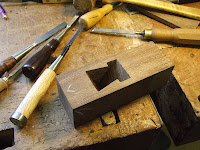
And here's a photo of the completed plane - and a sweet little thing she is too :)
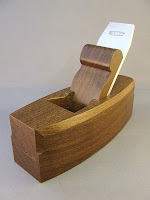
I've also started another guitar project - after seeing Paul Weller in action with his trusty '60's Gibson SG I had to have one. But after finding out the price I decided to build my own. I've keeping a photo diary here on my Philsville site.
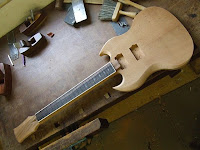
Next week sees me travelling to the States to Maine and the Lie-Nielsen factory. I'm really looking forward to this trip, a dream trip for me. Needless to say, I'll be taking plenty of photographs. And if you're attending the open day please come by my bench and say "hello!"
Cheers
Philly